Process Pumps
Supporting an evolving industrial base
with unique combinations
The world keeps evolving in fascinating ways.
Utilizing the wealth of technology and achievements we have cultivated over many long years, we are committed to the pursuit of optimized combinations of products for use all over the world, constructing a system capable of supporting the market’s needs.

Overhang Pump
Overhang pump compliant with API610 requirements
Featuring centerline support, the NSI is appropriate for many high-temperature applications.
Overview
Heavy-duty overhang pump compliant with API61 requirements.
Design Features
Featuring back pull-out construction.
Centerline support
The centerline support structure is designed to eliminate the effects of thermal expansion under high-temperature operating conditions.
Seal chamber
Seal chamber dimensions fully conform to API682 and API610 standards, with installation of dual seals also supported.
Air cooling system
Forced air-cooling by fan is standard for high-temperature applications. Operation up to maximum temperature of 250°C is possible without using cooling water on bearings. At temperatures over 250°C, a water jacket-cooling bearing housing is used.
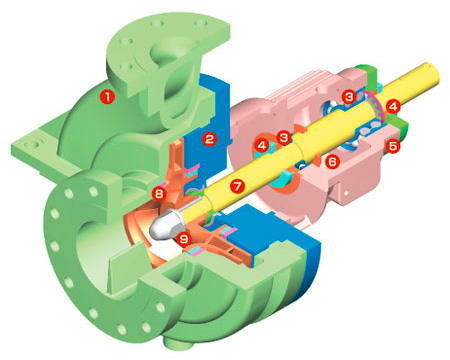
- 1Casing
-
The casing is designed in compliance with API610. Metal-to-metal fitting prevents misalignment, ensuring perfect sealing. The top centerline discharge design enables reliable self-venting.
- 2Seal chamber
-
The seal chamber is designed to comply with API682 and API610 standard dimensions.
- 3Bearings
-
Bearings are designed for a bearing life of at least 25,000 operating hours.
- 4Replaceable labyrinth end seals and deflectors
-
Labyrinth end seals and deflectors (non-sparking materials) effectively retain oil in the housing and prevent entry of foreign material into the housing.
- 5Bearing housing
-
The bearing housing is equipped with a constant level oiler.
- 6Lubrication
-
Bearings are lubricated using an oil flinger system.
- 7Bearings
-
Shaft rigidity complies with API682 and API610 requirements, minimizing shaft deflection and extending mechanical seal life.
- 8Replaceable wear rings
-
Both the casing and impeller are fitted with wear rings.
- 9Impeller
-
This model adopts a fully enclosed impeller designed for specific operating conditions with maximum efficiency and low NPSH.
The impeller is dynamically balanced to comply with API610 requirements.
Performance Chart
Coverage
- 50Hz
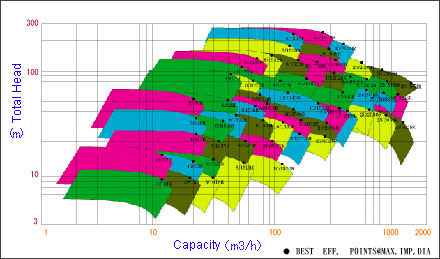
Coverage
- 60Hz
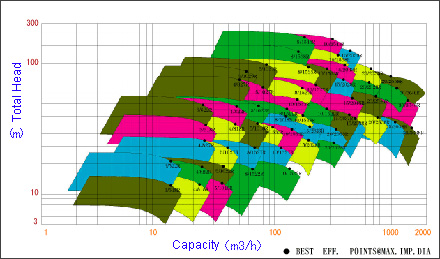
(*) In addition to the chart laid out above, we are happy to provide the ideal design for your company’s applications.
Specifications
- Maximum flow rate: 1500m³/h
- Maximum diff. head: 400m
- Maximum operating temperature:400℃
- Pressure rating:4MPa
Between Bearings Pump
Compliant with API610 requirements
Radially Split Multi-Stage Double Casing Between Bearings Pump
The BTBF (BTBFD) model is suitable for high pressures, high temperatures, and high speeds, as well as a broad range of other heavy-duty processes and industrial applications. Using double suction impellers (BTBFD), it is also suitable for low NPSH applications.
Overview
The BTBF model is a horizontal, radially split, multi-stage, single suction (BTBFD: double suction at 1st stage) between bearings double barrel pump with double casing, diffuser guide-vane, and centerline support.
The BTBF (BTBFD) model is suitable for high pressures, high temperatures, and high speeds, as well as a broad range of other heavy-duty processes and industrial applications.
Design Features
This is a heavy-duty pump conforming to API610 requirements.
Seal chamber
Seal chamber dimensions fully conform to API682 and API610 standards, with installation of our own standard-dimension dual seals also supported.
Easy maintenance
Overhaul can be performed without removal of main pipelines or drive assembly.
High reliability
Balance drum reduces thrust force to an optimum level. Diffuser guide vane provides balance for internal radial force.
Additionally, full-circular construction of the bearing housing and high-precision dynamic balance ensure stable operation and long bearing life.
Self-venting
Both the discharge and suction nozzles are located on top, which enables self-venting and achieves a smoother start-up.
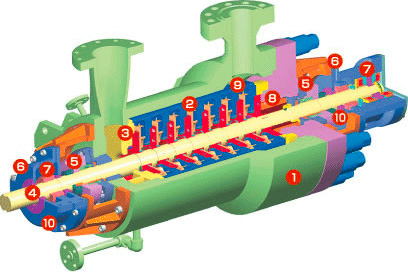
- 1Outer casing
-
The casing is designed in full compliance with API610 requirements (design pressure, nozzle external force, moment, etc.).
Cylindrical forging from high-grade steel grants the strength required for safe operations under high pressure up to maximum operating temperature.
The radially split outer casing is fitted metal-to-metal with a controlled compression gasket that ensures perfect sealing without misalignment. The centerline support design prevents misalignment caused by thermal expansion.
- 2Impeller
-
Designed for high efficiency and low NPSH, the enclosed single-suction (BTBFD: double suction at 1st stage) multi-stage impeller is designed to meet a wide range of specific operating conditions. The arrangement of impeller vanes and diffusers is designed to avoid vane-pulsation buildup.
The impeller is firmly secured to the shaft by interference fit and split rings.
The impeller is dynamically balanced to comply with API610 requirements.
- 3Wear rings
-
Fitted with replaceable wear rings.
- 4Main shaft
-
Minimizing main shaft deflection as far as possible prolongs bearing and seal life. The double keyway design of the main shaft makes balancing easier.
- 5Shaft seal and seal chamber
-
All seals and plans for mechanical seals comply with API682 and API610 requirements. Gland packing can be installed upon request.
Using a balance line, seal chamber pressure on both sides (coupling and anti-coupling side) is designed to maintain suction pressure for the mechanical seal.
- 6Bearing housing
-
Full circular bracket design minimizes any vibration of the bearing housing. Pump vibration is within the API610 permitted range. If operating at high temperatures, a suitable cooling system will be installed.
- 7Bearings
-
Bearing lubrication systems are available in three different configurations, all in compliance with API610 requirements, to meet various operating applications.
- 1.Ball radial and angular contact thrust
ball bearings / Oil bath - 2.Sleeve radial and angular contact thrust
ball bearings / Oil ring lubrication - 3.Sleeve radial and tilting pad thrust
bearings / Pressurized lubrication
- 1.Ball radial and angular contact thrust
- 8Balance drum
-
Balance drum reduces thrust force to an optimum level and prolongs bearing life.
- 9Inner casing
-
The precision-machined inner casing of forged steel improves machining accuracy, surface smoothness, and reliability of materials.
Intermediate covers with radial split and metal-to-metal fitting minimize internal leakages and misalignment.
Diffusers with multiple equally spaced vanes equalize pressure at all points around the impellers, providing radial force balance and, as a result, eliminating shaft deflection.
- 10Labyrinth end seals and deflectors
-
Replaceable labyrinth end seals and deflectors effectively retain oil in the housing and prevent entry of foreign material into the housing.
Performance Chart
Coverage
- 50Hz
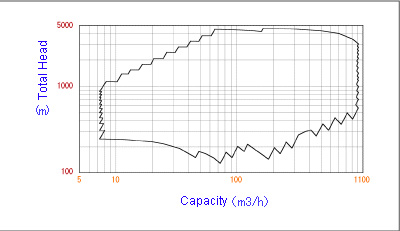
Coverage
- 60Hz
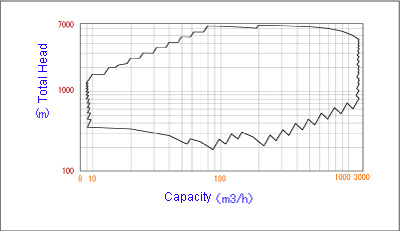
(*) In addition to the chart laid out above, we are happy to provide the ideal design for your company’s applications.
Specifications
- Maximum flow rate:1100m³/h
- Maximum discharge pressure:2500# Flange rating
- Maximum operating temperature:400℃
- Maximum speed:6000rpm
HTB (HTBD)
Axially Split Multi-Stage Between Bearings Pump
(API Class BB3)
Compliant with API610 requirements
Axially Split Multi-Stage Between Bearings Pump
Adopting a volute-type casing enables easy removal and inspection of rotors. Using double suction impellers (HTBD), it is also suitable for low NPSH applications.
Overview
The HTB model is a horizontal type axially split, multi-stage, single suction (HTBD: double suction at 1st stage), double volute between bearings pump with centerline support. The HTB (HTBD) model is suitable for high pressures and large capacities, as well as a wide range of processes and industrial applications.
Design Features
This is a heavy-duty pump conforming to API610 requirements.
Seal chamber
Seal chamber dimensions fully conform to API682 and API610 standards, with installation of our own standard-dimension dual seals also supported.
Compact design
Casing with compact crossovers minimizes friction loss on flow passages.
High reliability
The opposite impeller multi-stage arrangement provides pumps with balance for thrust force. Double volute casing provides balance for internal radial force.
Additionally, full-circular construction of the bearing housing and high-precision dynamic balance ensure stable operation and long bearing life.
Easy maintenance
Overhaul can be performed without removal of main pipelines or drive assembly. Adopting a volute-type casing enables easy removal and inspection of rotors.
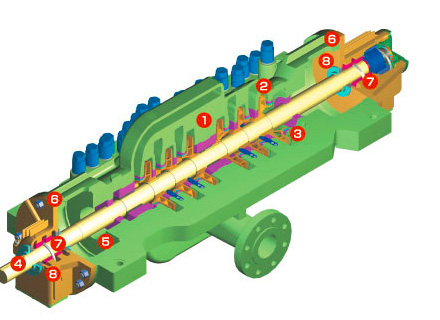
- 1Casing
-
The casing is designed in full compliance with API610 requirements (design pressure, nozzle external force, moment, etc.). Casing gaskets can be selected as appropriate to meet operating specifications and specific liquids to be used, ensuring reliable sealing performance.
The centerline support design prevents misalignment caused by thermal expansion. Suction and discharge nozzles are integrally cast with the lower part of the casing, enabling rotors to be taken out without removing the drive machine or pipelines.
The double volute design reduces radial force.
The volute casing is designed for easy removal and inspection of rotors.
- 2Impeller
-
Designed for high efficiency and low NPSH, the enclosed single-suction (HTBD: double suction at 1st stage) multi-stage impeller is designed to meet a wide range of specific operating conditions. The impeller is firmly secured to the shaft by interference fit and split rings to prevent deviations caused by axial thrust force.
The impeller is dynamically balanced to comply with API610 requirements. Adopting a multi-stage back-to-back impeller arrangement suppresses thrust load and prolongs bearing life.
- 3Wear rings
-
Fitted with replaceable wear rings.
- 4Main shaft
-
Main shaft deflection is minimized for longer bearing life and shaft seal life.
- 5Shaft seal and seal chamber
-
All seals and plans for mechanical seals comply with API682 and API610 requirements. Gland packing can be installed upon request.
Using a balance line, seal chamber pressure on both sides (coupling and anti-coupling side) is designed to maintain suction pressure for the mechanical seal.
- 6Bearing housing
-
Full circular bracket design minimizes any vibration of the bearing housing. Pump vibration is within the API610 permitted range. If operating at high temperatures, a suitable cooling system will be installed.
- 7Bearings
-
Bearing lubrication systems are available in three different configurations, all in compliance with API610 requirements, to meet various operating applications.
- 1.Ball radial and angular contact thrust
ball bearings / Oil bath - 2.Sleeve radial and angular contact thrust
ball bearings / Oil ring lubrication - 3.Sleeve radial and tilting pad thrust
bearings / Pressurized lubrication
- 1.Ball radial and angular contact thrust
- 8Labyrinth end seals and deflectors
-
Replaceable labyrinth end seals and deflectors effectively retain oil in the housing and prevent entry of foreign material into the housing.
Performance Chart
Coverage
- 50Hz
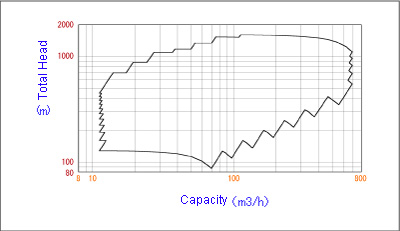
Coverage
- 60Hz
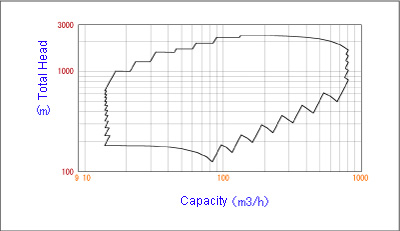
(*) In addition to the chart laid out above, we are happy to provide the ideal design for your company’s applications.
Specifications
- Maximum flow rate:750m³/h
- Maximum diff. head:2200m
- Maximum operating temperature:200℃
MMTB Axially Split Multi-Stage Between Bearings
Pump (API Class BB3)
Compliant with API610 requirements Axially Split Multi-Stage Between Bearings Pump
Featuring a precision-machined diffuser, this high-efficiency pump is suitable for applications from small flow rates.
Overview
The MTB model is a horizontal, axially split, multi-stage, single suction, between bearings process pump with diffuser guide-vane and centerline support.
The MTB is suitable for high pressures and a wide range of process applications.
Design Features
This is a heavy-duty pump conforming to API610 requirements.
Seal chamber
Seal chamber dimensions fully conform to API682 and API610 standards, with installation of our own standard-dimension dual seals also supported.
Easy Maintenance
Overhaul can be performed without removal of main pipelines or drive assembly.
High reliability
The multi-stage back-to-back arrangement of the impeller reduces thrust force to an optimum level. Diffuser guide vane provides balance for internal radial force.
Additionally, full-circular construction of the bearing housing and high-precision dynamic balance ensure smooth operation and long bearing life.
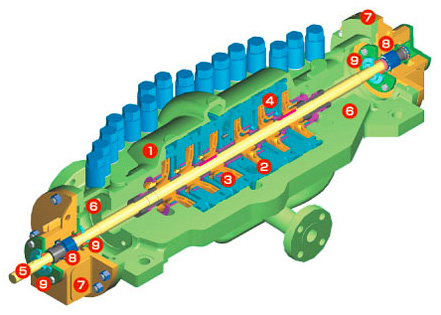
- 1Casing
-
The casing is designed in full compliance with API610 requirements (design pressure, nozzle external force, moment, etc.).
Casing gaskets can be selected as appropriate to meet operating specifications and specific liquids to be used, ensuring reliable sealing performance.
The centerline support design prevents misalignment caused by thermal expansion. Suction and discharge nozzles are integrally cast with the lower part of the casing, enabling rotors to be taken out without removing the drive machine or pipelines.
- 2Impeller
-
Designed for high efficiency, the enclosed single-suction multi-stage impeller is designed to meet a wide range of specific operating conditions.
Dynamic balance of the impeller conforms to API610 requirements.
Adopting a multi-stage back-to-back impeller arrangement suppresses thrust load and prolongs bearing life.
- 3Wear rings
-
Fitted with replaceable wear rings.
- 4Diffuser
-
The precision-machined diffuser guide-vane maintains high efficiency and provides radial force balance.
- 5Main shaft
-
Minimizing main shaft deflection as far as possible prolongs bearing and seal life. Conforms to API610 requirements.
- 6Shaft seal and seal chamber
-
All seals and plans for mechanical seals comply with API682 and API610 requirements. Gland packing can be installed upon request. Using a balance line, seal chamber pressure on both sides (coupling and anti-coupling side) is designed to maintain suction pressure for the mechanical seal.
- 7Bearing housing
-
Full circular bracket design minimizes any vibration of the bearing housing. Pump vibration is within the API610 permitted range. If operating at high temperatures, a suitable cooling system will be installed.
- 8Bearings
-
Bearing lubrication systems are available in three different configurations, all in compliance with API610 requirements, to meet various operating applications.
- 1.Ball radial and angular contact thrust
ball bearings / Oil bath - 2.Sleeve radial and angular contact thrust
ball bearings / Oil ring lubrication - 3.Sleeve radial and tilting pad thrust
bearings / Pressurized lubrication
- 1.Ball radial and angular contact thrust
- 9Labyrinth end seals and deflectors
-
Replaceable labyrinth end seals and deflectors effectively retain oil in the housing and prevent entry of foreign material into the housing.
Performance Chart
Coverage
- 50Hz
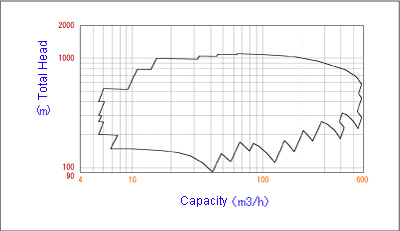
Coverage
- 60Hz
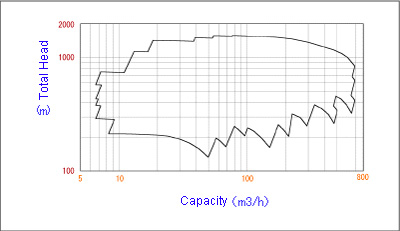
(*) In addition to the chart laid out above, we are happy to provide the ideal design for your company’s applications.
Specifications
- Maximum flow rate: 650m³/h
- Maximum diff. head: 1500m
- Maximum operating temperature: 200℃
RTH Axially Split Two-Stage Between Bearings Pump
(API Class BB1)
Compliant with API610 requirements
Axially Split Two-Stage Between Bearings Pump
The RTH model is suitable for low NPSH, large capacity, and medium pressure applications.
Overview
The RTH model is a horizontal, axially split, two-stage, single or double suction, double volute between bearings process pump with centerline support.
The RTH model is suitable for low NPSH, large capacity, and medium pressure applications.
Design Features
This is a heavy-duty pump conforming to API610 requirements.
Seal chamber
Seal chamber dimensions fully conform to API682 and API610 standards, with installation of our own standard-dimension dual seals also supported.
Easy maintenance
Overhaul can be performed without removal of main pipelines or drive assembly.
High reliability
The double volute casing design and double suction impeller, as well as the impeller rear alignment arrangement, reduce the radial force and thrust force balance of the pump, achieving stable operation and prolonging bearing life.
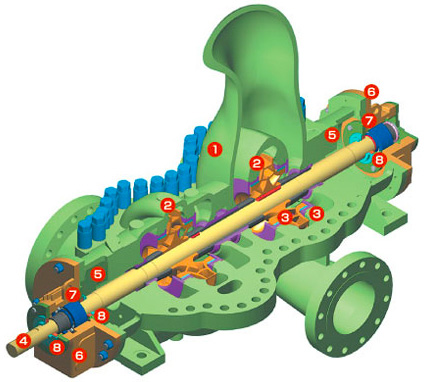
- 1Casing
-
The casing is designed in full compliance with API610 requirements (design pressure, nozzle external force, moment, etc.).
Casing gaskets can be selected as appropriate to meet operating specifications and specific liquids to be used, ensuring reliable sealing performance.
The centerline support design prevents misalignment caused by thermal expansion. Suction and discharge nozzles are integrally cast with the lower part of the casing, enabling rotors to be taken out without removing the drive machine or pipelines.
- 2Impeller
-
Designed for high efficiency and low NPSH, the enclosed single-suction/double-suction multi-stage impeller is designed to meet specific operating conditions. Dynamic balance of the impeller conforms to API610 requirements. Adopting a multi-stage back-to-back impeller arrangement or balanced double-suction configuration suppresses thrust load and prolongs bearing life.
- 3Wear rings
-
Fitted with replaceable wear rings.
- 4Main shaft
-
Minimizing main shaft deflection as far as possible prolongs bearing and seal life.
- 5Shaft seal
-
All seals and plans for mechanical seals comply with API682 and API610 requirements. Gland packing can be installed upon request.
- 6Bearing housing
-
Full circular bracket design minimizes any vibration of the bearing housing. Pump vibration is within the API610 permitted range. If operating at high temperatures, a suitable cooling system will be installed.
- 7Bearings
-
Bearing lubrication systems are available in three different configurations, all in compliance with API610 requirements, to meet various operating applications.
- 1.Ball radial and angular contact thrust
ball bearings / Oil bath - 2.Sleeve radial and angular contact thrust
ball bearings / Oil ring lubrication - 3.Sleeve radial and tilting pad thrust
bearings / Pressurized lubrication
- 1.Ball radial and angular contact thrust
- 8Labyrinth end seals and deflectors
-
Replaceable labyrinth end seals and deflectors effectively retain oil in the housing and prevent entry of foreign material into the housing.
Performance Chart
Coverage
- 50Hz
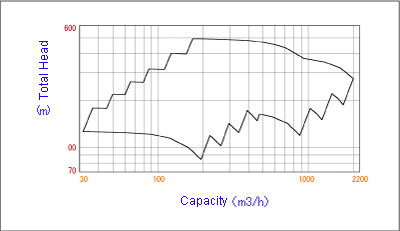
Coverage
- 60Hz
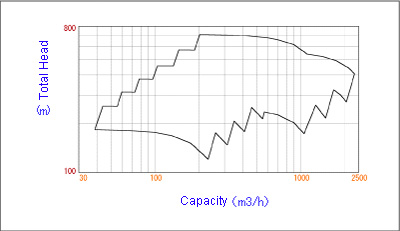
(*) In addition to the chart laid out above, we are happy to provide the ideal design for your company’s applications.
Specifications
- Maximum flow rate:2000m³/h
- Maximum diff. head: 650m
- Maximum operating temperature:200℃
RTV Radially Split Two-Stage Between Bearings
Pump (API Class BB2)
Compliant with API610 requirements Radially Split Two-Stage Between Bearings Pump
The RTV model is suitable for low capacity and medium pressure applications. It can also be used under high temperature conditions.
Overview
The RTV model is a horizontal, radially split, two-stage, single suction, diffuser (at 1st stage) and single or double volute (at 2nd stage) between bearings process pump with centerline support. The RTV is suitable for use at low and medium pressures.
Design Features
This is a heavy-duty pump conforming to API610 requirements.
Seal chamber
Seal chamber dimensions fully conform to API682 and API610 standards, with installation of our own standard-dimension dual seals also supported.
Easy maintenance
Overhaul can be performed without removal of main pipelines or drive assembly.
High reliability
The rear alignment arrangement of the impeller balances the thrust force of the pump. The volute casing with attached diffuser balances the internal radial force.
Additionally, full-circular construction of the bearing housing and high-precision dynamic balance ensure stable operation and long bearing life.
Self-venting
Both the discharge and suction nozzles are located on top, which enables self-venting and achieves a smoother start-up.
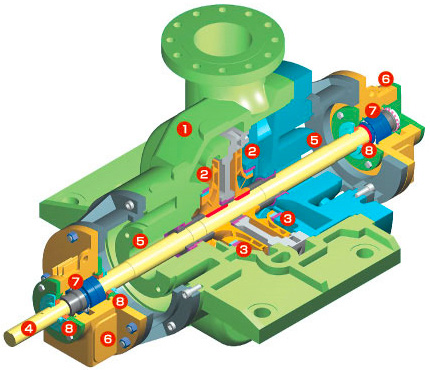
- 1Casing
-
The casing is designed in full compliance with API610 requirements (design pressure, nozzle external force, moment, etc.). The radially split outer casing is fitted metal-to-metal with a controlled compression gasket that ensures perfect sealing without misalignment. The centerline support design prevents misalignment caused by thermal expansion. The single head design with back pull out enables removal of rotors without needing to remove the drive assembly or suction/discharge pipelines.
- 2Impeller
-
Designed for high efficiency, the enclosed single-suction impeller is designed to meet specific operating conditions. The impeller is dynamically balanced to comply with API610 requirements. Adopting a back-to-back impeller arrangement suppresses thrust load and prolongs bearing life.
- 3Wear rings
-
Fitted with replaceable wear rings.
- 4Main shaft
-
Minimizing main shaft deflection as far as possible prolongs bearing and seal life.
- 5Shaft seal
-
All seals and plans for mechanical seals comply with API682 and API610 requirements. Gland packing can be installed upon request.
- 6Bearing housing
-
Full circular bracket design minimizes any vibration of the bearing housing. Pump vibration is within the API610 permitted range. If operating at high temperatures, a suitable cooling system will be installed.
- 7Bearings
-
Bearing lubrication systems are available in three different configurations, all in compliance with API610 requirements, to meet various operating applications.
- 1.Ball radial and angular contact thrust
ball bearings / Oil bath - 2.Sleeve radial and angular contact thrust
ball bearings / Oil ring lubrication - 3.Sleeve radial and tilting pad thrust
bearings / Pressurized lubrication
- 1.Ball radial and angular contact thrust
- 8Labyrinth end seals and deflectors
-
Replaceable labyrinth end seals and deflectors effectively retain oil in the housing and prevent entry of foreign material into the housing.
Performance Chart
Coverage
- 50Hz
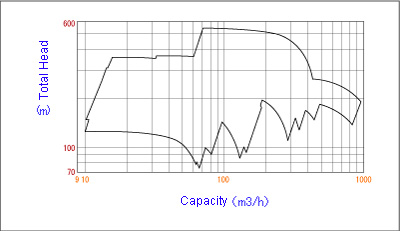
Coverage
- 60Hz
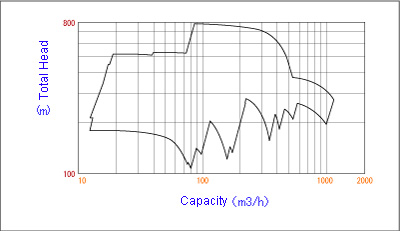
(*) In addition to the chart laid out above, we are happy to provide the ideal design for your company’s applications.
Specifications
- Maximum flow rate:500m³/h
- Maximum diff. head:750m
- Maximum operating temperature:400℃
HDV Radially Split Single-Stage Between Bearings
Pump (API Class BB2)
Compliant with API610 requirements Radially Split Single-Stage Between Bearings Pump
Featuring a double suction impeller, this model is suitable for use with large capacity and low NPSH applications. It can also be used under high temperature conditions.
Overview
The HDV model is a horizontal, radially split, single stage, double suction, double volute between bearings process pump with centerline support.
The HDV model is suitable for large capacity, low NPSH, and high temperature applications
Design Features
This is a heavy-duty pump conforming to API610 requirements.
Seal chamber
Seal chamber dimensions fully conform to API682 and API610 standards, with installation of our own standard-dimension dual seals also supported.
Easy maintenance
Overhaul can be performed without removal of main pipelines or drive assembly.
High reliability
The double suction impeller design balances thrust force, while the double volute casing reduces radial force. Additionally, full-circular construction of the bearing housing and high-precision dynamic balance ensure stable operation and long bearing life.
Self-venting
Both the discharge and suction nozzles are located on top, which enables self-venting and achieves a smoother start-up.
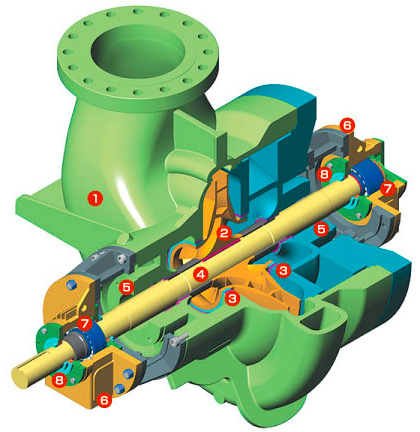
- 1Casing
-
The casing is designed in full compliance with API610 requirements (design pressure, nozzle external force, moment, etc.).
The radially split outer casing is fitted metal-to-metal with a controlled compression gasket that ensures perfect sealing without misalignment. The centerline support design prevents misalignment caused by thermal expansion.
The single head design with back pull out enables removal of rotors without needing to remove the drive assembly or suction/discharge pipelines. The double volute design reduces radial force.
- 2Impeller
-
Designed for high efficiency and low NPSH, the enclosed double-suction impeller is designed to meet specific operating conditions.
The impeller is dynamically balanced to comply with API610 requirements.
The well-balanced double suction design suppresses thrust load and prolongs bearing life.
- 3Wear rings
-
Fitted with replaceable wear rings.
- 4Main shaft
-
Minimizing main shaft deflection as far as possible prolongs bearing and seal life.
- 5Shaft seal
-
All seals and plans for mechanical seals comply with API682 and API610 requirements. Gland packing can be installed upon request.
- 6Bearing housing
-
Full circular bracket design minimizes any vibration of the bearing housing. Pump vibration is within the API610 permitted range. If operating at high temperatures, a suitable cooling system will be installed.
- 7Bearings
-
Bearing lubrication systems are available in three different configurations, all in compliance with API610 requirements, to meet various operating applications.
- 1.Ball radial and angular contact thrust
ball bearings / Oil bath - 2.Sleeve radial and angular contact thrust
ball bearings / Oil ring lubrication - 3.Sleeve radial and tilting pad thrust
bearings / Pressurized lubrication
- 1.Ball radial and angular contact thrust
- 8Labyrinth end seals and deflectors
-
Replaceable labyrinth end seals and deflectors effectively retain oil in the housing and prevent entry of foreign material into the housing.
Performance Chart
Coverage
- 50Hz
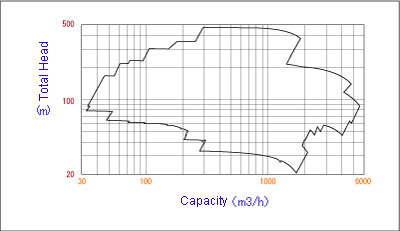
Coverage
- 60Hz
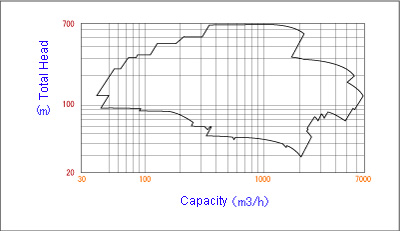
(*) In addition to the chart laid out above, we are happy to provide the ideal design for your company’s applications.
Specifications
- Maximum flow rate:3500m³/h
- Maximum diff. head:600m
- Maximum operating temperature:400℃
SD-S Axially Split Single-Stage Between Bearings Pump
(API Class BB1)
Compliant with API610 requirements Axially Split Single-Stage Between Bearings Pump (API Class BB1)
Featuring a double suction impeller design, this model is suitable for use with large capacity, low NPSH applications.
Overview
The SD-S model is a horizontal, axially split, single stage, double suction, double volute between bearings process pump with foot support.
The SD-S model is suitable for use with large capacity, low NPSH applications.
Design Features
This is a heavy-duty pump conforming to API610 requirements.
Seal chamber
Seal chamber dimensions fully conform to API682 and API610 standards, with installation of our own standard-dimension dual seals also supported.
Easy maintenance
Overhaul can be performed without removal of main pipelines or drive assembly.
High reliability
The double volute casing reduces radial force. The double suction impeller design balances thrust force. Additionally, full-circular construction of the bearing housing and high-precision dynamic balance ensure smooth operation and long bearing life.
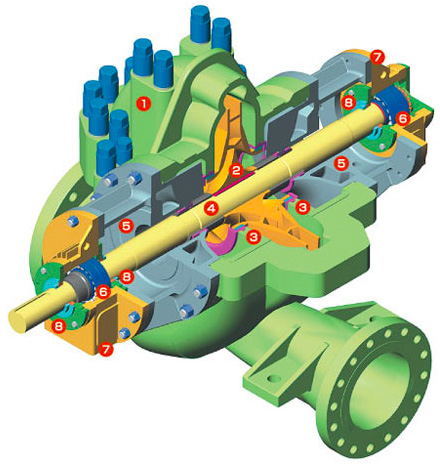
- 1Casing
-
The casing is designed in full compliance with API610 requirements (design pressure, nozzle external force, moment, etc.). Casing gaskets can be selected as appropriate to meet operating specifications and specific liquids to be used, ensuring reliable sealing performance.
Suction and discharge nozzles are integrally cast with the lower part of the casing, enabling rotors to be taken out without removing the drive machine or pipelines.
The double volute design reduces radial force.
- 2Impeller
-
Designed for high efficiency and low NPSH, the enclosed double-suction impeller is designed to meet specific operating conditions. The impeller is dynamically balanced to comply with API610 requirements.
The well-balanced double suction design suppresses thrust load and prolongs bearing life.
- 3Wear rings
-
Fitted with replaceable wear rings.
- 4Main shaft
-
Minimizing main shaft deflection as far as possible prolongs bearing and seal life.
- 5Shaft seal
-
All seals and plans for mechanical seals comply with API682 and API610 requirements. Gland packing can be installed upon request.
- 6Bearings
-
Bearing lubrication systems are available in three different configurations, all in compliance with API610 requirements, to meet various operating applications.
- 1.Ball radial and angular contact thrust
ball bearings / Oil bath - 2.Sleeve radial and angular contact thrust
ball bearings / Oil ring lubrication - 3.Sleeve radial and tilting pad thrust
bearings / Pressurized lubrication
- 1.Ball radial and angular contact thrust
- 7Bearing housing
-
Full circular bracket design minimizes any vibration of the bearing housing. Pump vibration is within the API610 permitted range. If operating at high temperatures, a suitable cooling system will be installed.
- 8Labyrinth end seals and deflectors
-
Replaceable labyrinth end seals and deflectors effectively retain oil in the housing and prevent entry of foreign material into the housing.
Performance Chart
Coverage
- 50Hz
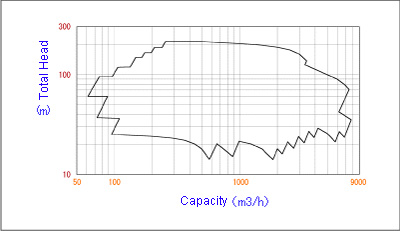
Coverage
- 60Hz
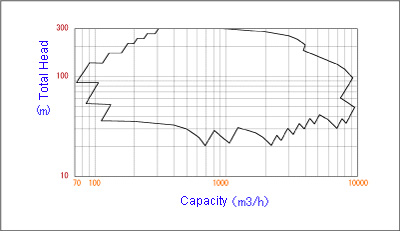
(*) In addition to the chart laid out above, we are happy to provide the ideal design for your company’s applications.
Specifications
- Maximum flow rate:9000m³/h
- Maximum diff. head:250m
- Maximum service temperature:150℃
CZ Vertically Suspended Double Casing Diffuser Pump
(API Class VS1 and VS6)
Compliant with API610 requirements Double Casing Vertical Pump
The CZ model is suitable for low temperatures and low NPSH, as well as a broad range of other heavy-duty processes and industrial applications. Removal of the external casing enables it to be used as a submerged-type pump.
Overview
The CZ model is a double casing, multi-stage vertical diffuser pump (API Class VS6).
Removal of the external casing enables it to be used as a submerged-type pump. (API Class VS1).
The CZ model is suitable for low temperatures and low NPSH, as well as a broad range of other processes and industrial applications. NPSH can be adjusted by adding a column component.
Design Features
This is a heavy duty pump conforming to API610 requirements.
Seal chamber
Seal chamber dimensions fully conform to API682 and API610 standards, with installation of our own standard-dimension dual seals also supported.
Space-saving and easy to install
The vertical pump configuration saves on valuable installation space. In-line construction means no complicated piping requirements.
Easy maintenance
Overhaul can be performed without removal of main pipelines or drive assembly.
High reliability
The drive mount and the pump case are optimally designed to ensure stable operation.
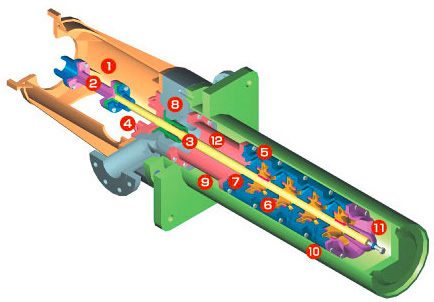
- 1Driver mount
-
Effectively designed to prevent vibrations generated by resonance.
- 2Spacer coupling
-
Spacer permits removal and repair of mechanical seals without removal of driver.
- 3Pump shaft
-
Outstanding strength and rigidity of pump shaft minimize deflection and vibrations.
- 4Shaft seal
-
All seals and plans for mechanical seals comply with API682 and API610 requirements. Gland packing can be installed upon request.
- 5Impeller
-
Designed for high efficiency and low NPSH, the enclosed multi-stage impeller is designed to meet a wide range of specific operating conditions. The impeller is dynamically balanced to comply with API610 requirements.
- 6Wear rings
-
Fitted with replaceable wear rings (on the fixed side only).
- 7Internal bushing
-
The optimum design of the closed clearance bushing minimizes pump shaft deflection. These bushings are lubricated by pumped liquid (as standard). Optionally, bushings can also be lubricated by an external source.
- 8Head
-
Designed in full compliance with API610 requirements (design pressure, nozzle external force, moment, etc.).
Head is constructed of superior-quality forged or fabricated steel, optimized for use with casings.
- 9Bowl
-
Equipped as standard with casing diffuser bowl. Optionally, precision-machined diffuser vane bowl can also be fitted. This maintains a high level of efficiency.
- 10Outer case
-
Length, diameter, and wall thickness are designed to suit operating conditions.
- 11Lower bearing and suction bell mouth
-
Suction bell mouth is designed to facilitate more efficient flow into the first stage impeller. The lower bearing functions as a pump shaft guide for alignment and concentricity.
- 12Column (optional)
-
If NSPH is extremely low, a column can be attached to handle this.
Performance Chart
Coverage
- 50Hz
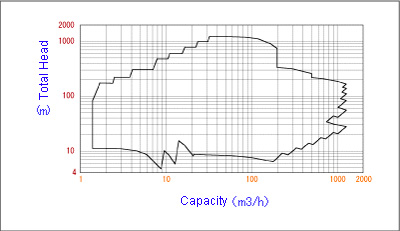
Coverage
- 60Hz
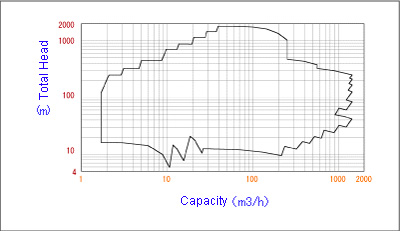
(*) In addition to the chart laid out above, we are happy to provide the ideal design for your company’s applications.
Specifications
- Maximum flow rate:1200m³/h
- Maximum diff. head:1500m
- Maximum operating temperature:150℃
- Minimum operating temperature:-120℃
SIW Line-Shaft Vertical Sump Pump
(API Class VS4)
Compliant with API610 requirements
Vertical sump pump
Since the impeller is situated underwater, it avoids the need to eliminate priming water or air. The range also includes a model (SIWN model) that does not require shaft seals.
Overview
The SIW model is a single stage, closed single-suction, volute type, line shaft vertical pump. The range also includes a model (SIWN model) that does not require mechanical shaft seals. Since this model requires no mechanical seals, it cuts down on initial cost and maintenance costs. This model is suitable for operating conditions involving non-hazardous materials and non-flammable fluids.
A semi-open impeller-type pump (SIWO model) is also available, which is suitable for use as a drainage pump for pits.
Design Features
This is a heavy duty pump conforming to API610 requirements.
Seal chamber
Seal chamber dimensions fully conform to API682 and API610 standards, with installation of our own standard-dimension dual seals also supported.
Easy startup and operation
As this pump is usually under flooded suction, it avoids the need to eliminate priming water or air.
Easy maintenance
Features a flanged spigot fit for casing and column in order to maintain alignment and facilitate easier maintenance.
High reliability
A powerful driver mount design ensures stable pump operation.
Space-saving and easy to install
The vertical pump configuration saves on valuable installation space. Shipment of the preassembled pump (excluding the driver) simplifies on-site installation work.
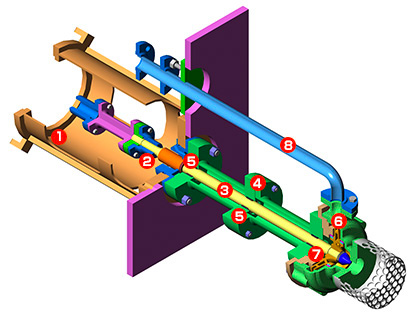
- 1Driver mount
-
Effectively designed to prevent vibrations generated by resonance.
- 2Shaft seal
-
All seals and plans for mechanical seals comply with API682 and API610 requirements. Gland packing can be installed upon request.
- 3Pump shaft
-
Outstanding strength and rigidity of pump shaft minimize deflection and vibrations.
- 4Column
-
Flanged spigot fit maintains precise alignment and as a result, prolongs bearing life. In the absence of a shaft seal, the pumped liquid does not fall to the bottom (floor level) as it leaves the hole at the top of the column pipe.
- 5Line shaft bearings
-
Closed clearance bushings minimize pump shaft deflection.
These bushings are lubricated by pumped liquid (as standard).
Optionally, bushings can also be lubricated by an external source.
- 6Impeller
-
Designed for high efficiency, the enclosed or semi-open suction impeller is designed to meet a wide range of specific operating conditions. The impeller is dynamically balanced to comply with API610 requirements.
- 7Wear rings
-
Fitted with replaceable wear rings (on the fixed side only).
- 8Discharge pipe
-
Discharge pipe is locked to the base plate, providing structural rigidity and minimizing vibration of the unit.
Performance Chart
Coverage
- 50Hz
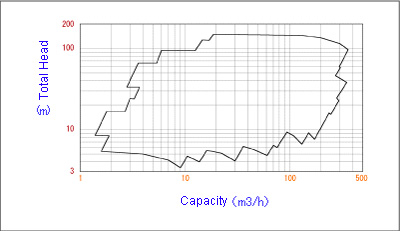
Coverage
- 60Hz
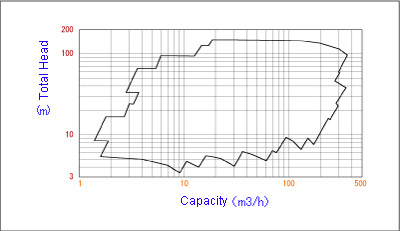
(*) In addition to the chart laid out above, we are happy to provide the ideal design for your company’s applications.
Specifications
- Maximum flow rate:400m³/h
- Maximum diff. head:150m
- Maximum service temperature:250℃
HPRT Hydraulic Power Recovery Turbine
Efficiently utilize energy during liquid transport
Installing a hydraulic power recovery turbine when transporting liquid from high pressure to low pressure enables more efficient utilization of energy by extracting rotational power from liquid pressure.
Overview
In oil refineries and petrochemical plants, after raw materials are sent to react or decompose in high-pressure tanks, the products of these processes are commonly returned to lower-pressure tanks. When fluids are transferred to high-pressure tanks, pumps impart energy to the fluid; however, that same energy is wasted if pressure-reducing valves or other throttle mechanisms are used when transferring fluids back to low-pressure tanks. Installing a hydraulic power recovery turbine (HPRT) when transporting fluids from high pressure to low pressure enables more efficient utilization of energy by extracting rotational power from liquid pressure.
Although we call these hydraulic power recovery turbines, their basic architecture is no different from a pump. The difference is that the direction of fluid flow is completely opposite to that of a pump. An HPRT sends high-pressure fluid to the discharge nozzle and out of the suction nozzle, applying turning force to the impeller in the reverse direction, which can be collected as power. For this reason, most devices sold as pumps can also be utilized as hydraulic power recovery turbines.
SNM also manufactures a hydraulic power recovery turbine, thus helping companies around the world conserve energy to prevent combat global warming.
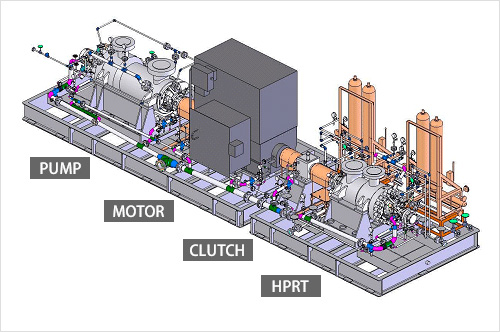