Steam Turbines
Advanced technology with reliability and performance—responding to the demands of the times.
We have a proven track record of delivering countless small- and medium-sized steam turbines to satisfy customer needs across the world. The excellent performance of our high-efficiency, energy-saving turbines for in-house power generation and our mechanical turbines for driving compressors in particular has won high acclaim.
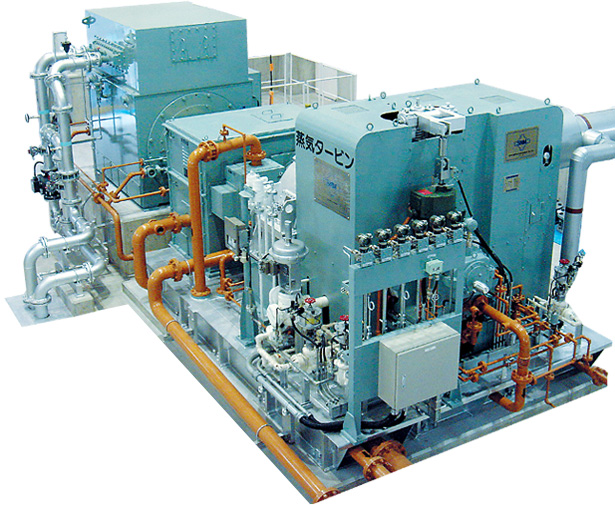
Condensing Turbines (Type C Multi-Stage)
High-efficiency, high-output multi-stage turbines
Converting exhaust pressure to a vacuum, Condensing multi-stage turbines can convert the heat energy of steam to mechanical energy without waste. Parts are standardized and easy to replace.
Overview
This condensing multi-stage turbine is a high-efficiency, high-output type capable of converting the heat energy of steam to mechanical energy without waste, converting turbine exhaust pressure as a vacuum.
This series is known as a multi-stage type, featuring at least two turbine blades attached to the shaft. The number of turbine stages and the average pitch diameter of these turbine blades are determined optimally in each case, depending on factors such as output, number of revolutions, intake steam pressure, temperature, exhaust pressure, and so on.
According to the number of stages selected, the nozzles, wings, turbine blades, shafts, housing, etc. are all subject to change, but all other essential parts are completely standardized and designed for easy attachment to any model. In addition, we maintain an abundant inventory of these standard parts and manage these to ensure they can be supplied quickly and reliably.
-
Condensing Multi-Stage Steam Turbines (upward-oriented exhaust) -
Condensing multi-stage steam turbine (downward-oriented Exhaust)
High Performance Steam Turbine with Interacted Shroud Type Blade
To improve turbine efficiency, we increase the annular area of the wing and reduce exhaust losses by lengthening blade length for the row of blades in the last stage. Speeding up the turbine and reducing the number of turbine stages are also effective for reducing the initial amount of investment.
For our high performance steam turbine with interacted shroud-type blade, we increased the annular area of the final stage’s row of blades to 1.6 times that of the conventional machine, and achieved a high-speed rotation of 125% with the same performance as the conventional model. As a result, given this emphasis on efficiency, this machine is more efficient than conventional machines at a lower price while providing the same performance as conventional machines, prioritizing selection for initial investment value.
Features
- (1) Priority selection for efficiency
-
- · Improved efficiency by enlarging the final annular area
- · Final annular area ratio 1.6 times greater (than conventional model)
- (2) Priority selection for initial investment (selection with reducing device)
-
- · Improved rotation speed: of 125% (compared to the company's own conventional models)
- · Turbine stage reduction rate of 10–20% (compared to the company's own conventional models)
- (3) General
-
- · Improving vibration resistance of blades by adopting blade that maintains all-round contact (interacted shroud type blade)
- · Using stellite welding for final-stage blades (standard measure against dampness)
- · Reducing exhaust hood losses by adopting a new exhaust case (housing)
- · First stage shroud-type injection option also available

Use
In recent years, environmental problems caused by global warming have resulted in calls for energy conservation, and fields of renewable energy such as biomass, cogeneration, and solar power are now being promoted. This model is often used for power recovery in such fields.
There are countless applications in other fields as well. As well as power generation for IPP (independent power production) and combined cycle plants, these turbines are suitable for private power generation across a variety of industries, including petrochemical production, petroleum refining plants, driving high-speed gas compressors in ammonia and ethylene plants, as a water supply pump for high-temperature high-pressure boilers as well as boiler induction fans, forced draft fans, as a compressed air source for plants and factories to drive compressors, and in sugar factories, paper mills, plywood factories, and others.
Also suitable for use with API standards 611, 612.
Main items
Model | Condensing steam turbine |
---|---|
Maximum output (kW) | 100,000 |
Maximum intake steam pressure (kgf/cm2g) | 130 |
Maximum intake steam temperature (°C) | 550 |
Maximum exhaust pressure (vacuum to maximum) (kgf/cm2g) | 1 |
Exhaust outlet direction | Upward, downward, axial flow |
Condensing turbines (multi-stage axial exhaust turbines)
Condensing steam turbines with improved development offering easier layout
Exhaust can be discharged along the axial direction and condensers can be connected directly. The simple layout contributes greatly to lower installation costs and running costs.
Overview
The axial exhaust type is an improved system with easier layout for developing condensing steam turbines. Although conventional condensing steam turbines orient the exhaust flow downward or upward in a direction perpendicular to the axis for return to the condenser, exhaust loss can be reduced by directing the exhaust along the direction of axial flow, which greatly improves energy efficiency.
Also, in terms of layout, the conventional design requires more space in the downward or upward direction. Our axial exhaust turbine is designed to discharge the exhaust axially and connect to the condenser directly, making layout easier. This can drastically reduce installation costs, and can greatly contribute to reduction of time and costs for maintenance and inspection.
- ・USA,OHIO
- ・MFR.NO.11358
- ・C11-R16-EX
- ・GENERATOR DRIVE
- ・67000kW
- ・3600RPM
- ・Max IN-P 1555 psia x 1000F (111.5 BarA x 538 ℃)SLIDING PRESS, CTL
- ・EXH-P 1.35 psia(0.097 Bar.A)
- ・2 Bleed Extractions
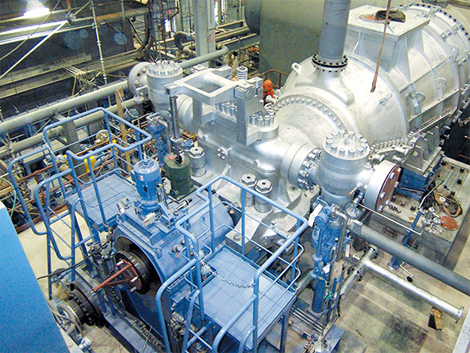
Considering how to best use kinetic energy has led to turbines with greatly improved energy efficiency.
Opened state
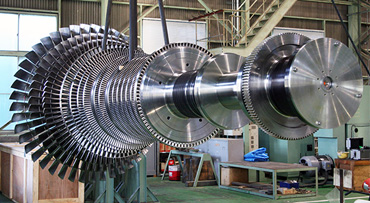
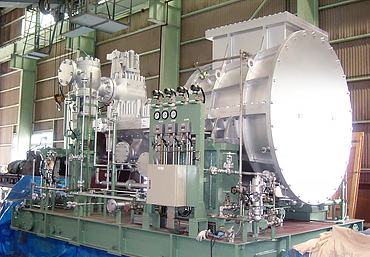
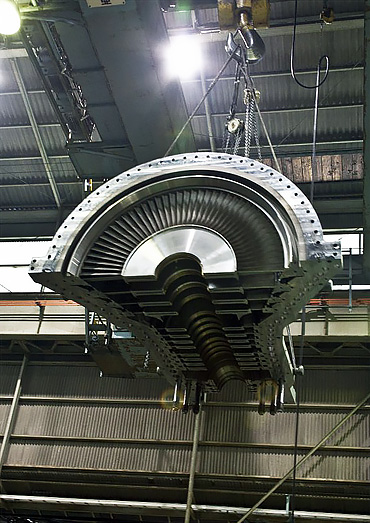
Advantages of axial exhaust turbines
1. Better mechanical efficiency
By adopting an axial exhaust design, exhaust losses can be reduced compared to the downward (or upward)-oriented exhaust models, and more efficient performance can be obtained.
This is verified using flow analysis of exhaust flows inside the exhaust hood.
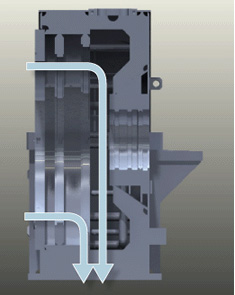
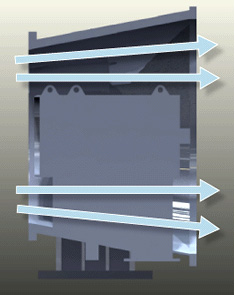
2. Cost reduction
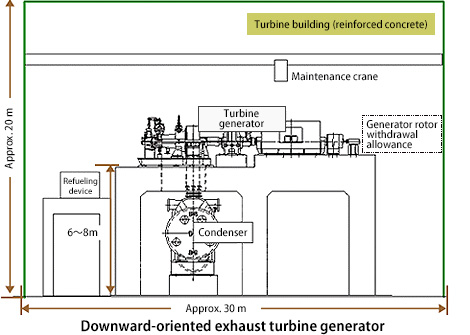

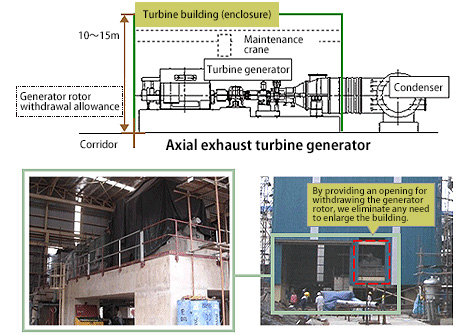
Advantages compared to downward-oriented exhaust turbines
Can be installed (including condenser) on flat surfaces, enabling drastically reduced construction costs for foundations and buildings.
- · Comparing ground level installation, foundational concrete usage is cut by about 30%
- · Building floor area is 1/4, building volume is 1/3
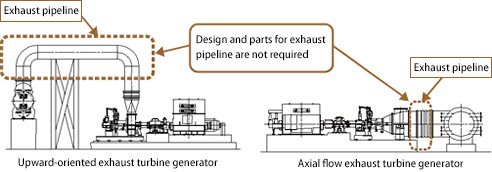
Advantages compared to upward-oriented exhaust type
Design and parts for exhaust pipeline are not required, and pedestals/support racks are also unnecessary, enabling significant reductions in cost.
Note: Listed values are examples only, and are not necessarily applicable in every case.
3. Shorter construction periods, other benefits
Advantages compared to downward-oriented exhaust turbines
By reducing the volume of foundation concrete and building volume, construction periods can be shortened.
Advantages compared to upward-oriented exhaust turbines
Enables easier maintenance and eliminates space required for maintenance.
Internal extraction pressure control type
Reusing thermal energy from exhaust steam
Utilizing the pressure differential between intake steam and expelled steam, part of the thermal energy is converted to mechanical energy and reused for the factory’s processes.
Overview
If steam is extracted from the intermediate stages of the turbine and sent to the factory, it is possible to achieve steady pressure from low turbine loads up to the specification by controlling internal extraction pressure.
Internal extraction pressure control is a method that uses a pressure control valve installed inside the casing of the turbine to perform pressure control on the “upstream” side of the valve, keeping extraction pressure constant.
Since up to 2 internal control valves can be installed, it is possible to extract two steam supply lines (medium-pressure steam, low-pressure steam) for the factory from a single turbine.
-
Single-stage internal extraction turbine -
Two-stage internal extraction turbine
Back pressure type (multi-stage B type)
Essential parts standardized for easy maintenance
According to the number of stages selected, the nozzles, wings, turbine blades, shafts, housing, etc. are all subject to change, but all other essential parts are completely standardized and designed for easy attachment to any model.
Overview
Back pressure turbines utilize the pressure differential between the intake steam and the expelled steam to efficiently convert part of the thermal energy of the steam into mechanical energy. The exhaust pressure is designed to be higher than atmospheric pressure, and the heat energy of the exhaust steam is reused for the factory’s processes.
This series is known as a multi-stage type, featuring at least two turbine blades attached to the shaft. The number of turbine stages and the average pitch diameter of these turbine blades are determined optimally in each case, depending on factors such as output, number of revolutions, intake steam pressure, temperature, exhaust pressure, and so on.
According to the number of stages selected, the nozzles, wings, turbine blades, shafts, housing, etc. are all subject to change, but all other essential parts are completely standardized and designed for easy attachment to any model. In addition, we maintain an abundant inventory of these standard parts and manage these to ensure they can be supplied quickly and reliably.
-
Back pressure steam turbine (downward-oriented exhaust type): No load, -
continuous testing Back pressure steam turbine (downward-oriented exhaust type) Photo shows on-site operation -
Back pressure steam turbine (upward-oriented exhaust type)
Uses
These turbines are suitable for private power generation across a variety of industries, including biomass and cogeneration, petrochemical production, petroleum refining plants, driving high-speed gas compressors in ammonia and ethylene plants, as a water supply pump for high-temperature high-pressure boilers as well as boiler induction fans, forced draft fans, as a compressed air source for plants and factories to drive compressors, and in sugar factories, paper mills, plywood factories, and others.
Also suitable for use with API standards 611, 612.
Main Products
Model | Back pressure multi-stage steam turbine (Type B) |
---|---|
Maximum output (kW) | 50,000 |
Maximum intake steam pressure (kgf/cm2g) | 130 |
Maximum intake steam temperature (°C) | 550 |
Maximum exhaust pressure (vacuum to maximum) (kgf/cm2g) | 35 |
Exhaust outlet orientation | Upward, downward, horizontal |
Back pressure type (single-stage horizontal placement/vertical placement)
This single-stage, horizontal-type compact general-purpose turbine is one of our leading models.
Both the H series and the high-output, high-speed compatible HO series are single-stage, horizontally-installed compact general-purpose turbines. Our product range also includes the high-speed rotation-compatible CC series for use with compressors, etc. and the vertical-type V series.
Overview
Both the H series and the high-output, high-speed compatible HO series are single-stage, horizontally-installed compact general-purpose turbines. Our product range also includes the high-speed rotation-compatible CC series (also single-stage and horizontally-installed) for use with compressors, etc. The vertical-type V series is also available.
Uses
Mainly used for pumps, fans, compressors, mills, and shredders in various factories such as petroleum plants, chemical plants, sugar mills, and power plants.
The H, HO, V series are suitable for use with the API 611 standard, while the CC series is suitable for use with the API 612 standard.
Main Products
Type H compact horizontal steam turbine
Back pressure single-stage steam turbine (Type H) | ||||
---|---|---|---|---|
Model | H-133 | H-142 | H-163 | H-183 |
Maximum output (kW) | 300 | 600 | 1,000 | 1,500 |
Maximum intake steam pressure (kgf/cm2g) | 45 | 45 | 45 | 45 |
Maximum intake steam temperature (°C) | 450 | 450 | 450 | 450 |
Maximum exhaust pressure (vacuum to maximum) (kgf/cm2g) | 7 | 7 | 7 | 7 |
Type HO compact horizontal steam turbine
Back pressure single-stage steam turbine (Type HO) | |||
---|---|---|---|
Model | HO142 | HO163 | HO183 |
Maximum output (kW) | 600 | 1,500 | 2,500 |
Maximum intake steam pressure (kgf/cm2g) | 67 | 67 | 67 |
Maximum intake steam temperature (°C) | 500 | 500 | 500 |
Maximum exhaust pressure (vacuum to maximum) (kgf/cm2g) | 15 | 24 | 12 |
Type CC single-stage steam turbine
Model | CC-400 | CC-401 | CC-600 | CC-601 | CC-800 | CC-802 |
---|---|---|---|---|---|---|
Maximum output (kW) | 2,000 | 1,500 | 3,000 | 2,000 | 3,000 | 3,000 |
Maximum intake steam pressure (kgf/cm2g) | 67 | 67 | 67 | 67 | 67 | 67 |
Maximum intake steam temperature (°C) | 500 | 500 | 500 | 500 | 500 | 500 |
Maximum exhaust pressure (vacuum to maximum) (kgf/cm2g) | 15 | 15 | 15 | 15 | 12 | 12 |
Type V vertical steam turbine
Back pressure single-stage steam turbine | ||
---|---|---|
Model | V-136 | V-145 |
Maximum output (kW) | 300 | 500 |
Maximum intake steam pressure (kgf/cm2g) | 45 | 45 |
Maximum intake steam temperature (°C) | 450 | 450 |
Maximum exhaust pressure (from vacuum to maximum) (kgf/cm2g) | 7 | 7 |